
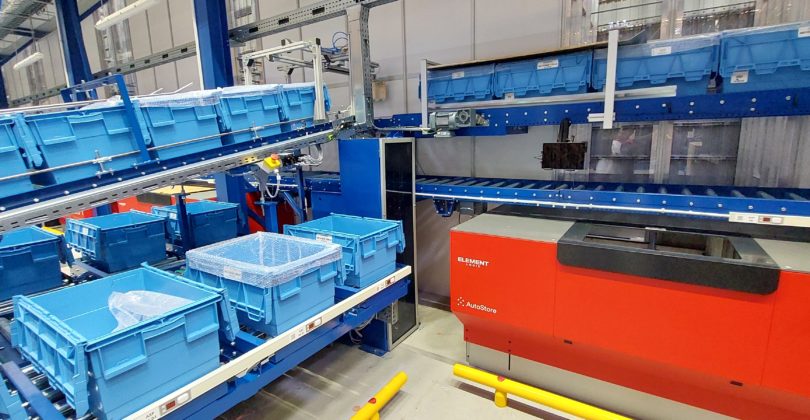
Euromedia Group Conveyor System – AutoStore technology operator, packing and dispatching of shipments
We have supplied a complex conveyor system, which ensures the operation of the robotic warehouse and downstream operations during packaging and dispatching of shipments. The customer is the leader of the Czech book market, Euromedia Group a.s., which operates the Luxor bookstore chain.
We also have experience with the link to AutoStore technology from other projects we have implemented.
Euromedia Group a.s. (EMG) has decided to significantly strengthen the capacity of storage and dispatch of book goods by building a new storage capacity in the Stochov logistics park. The new modern robotic warehouse occupies an area of over 10,000 square metres and up to 90 robots are helping to prepare the 9 million books stored here for dispatch.
Several cooperating companies were involved in the construction. At the heart of the solution is the Autostore robotic warehouse (Element Logic), the dynamic mySTOCK® WMS and myFABER® WES (Kvados) are the brains and the TMT large-scale conveyor system is the hands.
The contract was signed at the end of 2022, and the handover of the large-scale line for trial operation took place in mid-October 2023.
Description of the conveyor system
The installed AutoStore (hereafter referred to as AS) warehouse contains 65,000 plastic crates in the first phase and is now equipped with 16 ports out of the target 24 around the perimeter. The conveyor system ensures the supply of empty crates to the picking workstation at the ports, the transport of the crates from the ports to other storage areas, the transfer to the packing workstation and the subsequent dispatch with sorting of the shipments.
The picking process starts with the workstations located among the AS ports, where the operator manually places the picked goods into the INTEGRA plastic crates. The backbone route then optionally continues through parallel warehouse capacities (catchment racks “Bestsellers”, local “Kardex”), where any additional goods are loaded. After the automatic weighbridge, the transport is then split into two branches.
Big Box transport route
The first route continues to the Big Box workplace, where part of the product range is repackaged by hand from plastic crates into paper boxes. This is followed by a manual crate/box sealing workstation, after which automatic strapping takes place. The transport route ends with the outbound sorter, where the goods are automatically sorted into drop bins according to the individual transport companies or distribution directions.
Small Box transport route
The second branch goes to the Small Box workstation, where all goods are manually unloaded from the boxes and sorted into individual orders. Here, some items are packed by hand into envelopes. Most of the items, however, go to the automatic Carton Wrap machine (hereinafter referred to as CW), which had to be implemented in the project, including SW communication. From the Small Box workstation, three separate outgoing transport routes run above each other in order from the bottom: the empty INTEGRA boxes are taken via another automatic weighing machine and a raised buffer back to the AS ports, the envelopes are taken for dispatch, and the unwrapped goods are taken to the CW.
Output route
The output route of the packed paper boxes from CW is then connected to the transport route of the envelopes to form one common material flow towards the dispatch sorter. Here, as in the previous case, the goods are sorted into catchment bins (stainless steel slides) according to the individual transport companies or distribution routes.
Specification of the transported goods and performance parameters of the line
Unloading into plastic crates from the AutoStore
- Conveyed loads – plastic crates INTEGRA
- Dimensions of individual packages – 600 × 400 × 330 mm
- Weight of crates – min. 2 kg/pc max. 25 kg/pc
- Takt of picking points – 16 picking points with 60 pcs/hr.
- Transport capacity of the backbone route – max. 1,200 pcs/hr.
Dispatch – paper boxes + INTEGRA boxes
- Conveyed loads – plastic INTEGRA boxes + paper boxes
- Dimensions of individual packages – crates 600 × 400 × 330 mm, boxes 600 × 400 × 100 – 300 mm
- Weight of loads – min. 2 kg/pcs max. 25 kg/pcs
- Dispatch sorter output – max. 600 pcs/hr.
Dispatch from automatic packing (Carton Wrap) + boxes and envelopes from manual packing
- Conveyed loads – cartons, envelopes
- Dimensions of individual packages – min. 240 × 150 × 30 mm, max. 600 × 400 × 370 mm
- Weight of loads – min. 0.2 kg, max. 11 kg/pc
- Dispatch sorter output – max. 2400 pcs/hr.
Service
We provide both regular and emergency service to the line in 24/7 mode.
Is this an interesting project for you? ? If you have any questions, you can contact us.
Read more about how conveyor systems work in warehouses and distribution centres.